熱繡寶
熱鏽寶處理係由第一層金屬亞鉛層,第二層高耐食性化成皮膜層,第三層以石膏系材為原料。
熱鏽寶的特徵為表面燒成層和化成皮膜層以架橋效果般強固連結而成。又金屬亞強韌複合皮膜。熱鏽寶其防鏽性能,不同一般的單一物質表面處理,其由三層的相乘作用形成卓越的綜合耐蝕性能。
專利 第1526310號 專利 第1570203號
性能
試驗項目 | 試驗成績 | 試驗方法 |
塗裝硬度 | 4H以上 | 鉛筆硬度(剝離測定) |
密著試驗 | 無異狀 | 以黏度強膠布貼於已有割痕1mm寬之十字面上後撕起 |
耐酸性 | 無異狀 | 5%硫酸、24小時浸漬 |
耐鹼性 | 無異狀 | 5%水酸化氫化鈉、72小時浸漬 |
耐熱性 | 無異狀 | 250度C,1小時放置 |
促進耐候性 | 無紅銹發生 | 1000小時,置於紫外線狀態下 |
別種金屬接觸腐蝕 | 很明顯的優於電鍍和熱浸鍍鋅 | 測完鹽水噴霧試驗之物品(JIS Z 2371),綁於不鏽銅物品 |
處理種類
種類 | 性能 | 顏色選擇 |
熱鏽寶第1級 | 鹽水噴霧500小時,亞硫酸(0.2l)15回 DIN 50018 | 銀白色、灰色、黑色、其他色 |
熱鏽寶第2級 | 鹽水噴霧1000小時,亞硫酸(0.2l)15回 DIN 50018 | 銀白色、灰色、黑色、其他色 |
熱鏽寶第3級 | 鹽水噴霧1000小時,亞硫酸(2.0l)15回 DIN 50018 | 灰色、黑色 |
熱浸鍍鋅、熱鏽寶 | 鹽水噴霧1000小時,亞硫酸(0.2l)15回 DIN 50018 | 銀白色、灰色、黑色、其他色 |
皮膜和防鏽架構
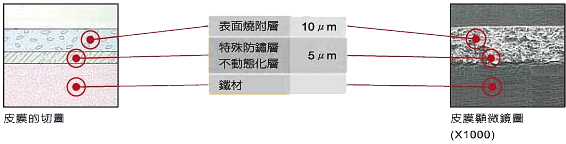
皮膜層 | 防鏽結構 |
表面燒附層 | 包含以強韌防鏽材料皮膜 |
特殊防鏽皮膜層 | 腐蝕因子被塗裝漆之特殊伸縮性和附著性抑制 |
不動態化層 | 熱鏽寶材料中包含不動態皮膜附於鍍層 |
RUSPERT
RUSPERT metal finish is the metal surface processing technology of high grade anti-corrosion consisting of 1st layer ; metallic zinc layer,2nd layer, high grade anti-corrosion chemical conversion film, and 3rd layer, baked ceramic surface coating.
The feature of RUSPERT is to join baked ceramic surface coating and chemical conversion film tightly together owing to bridging effect.
Furthermore, these layers are tightly joined together by means of chemical reactions, and such unique layer-combination brings stiff and fine combined coating films. RUSPERT treatment is not anti-corrosion by s single material, but by synergism of three layers, with which super rustproof quality is endowed.
Patent No. 1526310 Patent No. 1570203
Performance
Test item | Test result | Test method |
Hardness of paint film | Over 4H | Pencil hardness (peeling test) |
Adhesion | Nothing abnormal | Peeling test by adhesive tape on cross scribed test piece in 1mm width |
Acid resistance | Nothing abnormal | Immersion in 5% sulfuric acid solution for 24h |
Alkali resistance | Nothing abnormal | Immersion in 5% sodium hydroxide solution for 72h |
Heat resistance | Nothing abnormal | Exposure to 250°C heat for 1h |
Accelerated weathering | Free from red rust | In sunshine weather-0-meter for 1000h |
Contact corrosion to other metals | Obviously superior to galvanization(colored
chromating)and hot dip galvanizing. |
Corrosive investigation after Salt Mist Spray Test(JIS Z 2371)done comparatively on surface-treated steel bolts/nuts tightened on the stainless steel plate. |
Type of Processings
Type | Performance | Color Selection |
RUSPERT type I | S.S.T.500h
DIN 50018(0.2L)15 cycles |
Silver, Grey, Black, Other colors |
RUSPERT type II | S.S.T.1000h
DIN 50018(0.2L)15 cycles |
Silver, Grey, Black, Other colors |
RUSPERT type III | S.S.T.1000h
DIN 50018(2.0L)15 cycles |
Grey, Black |
RUSPERT on hot dip galvanizing | S.S.T.1000h
DIN 50018(0.2L)15 cycles |
Silver, Grey, Black, Other colors |
Coating and Rustproof Structure
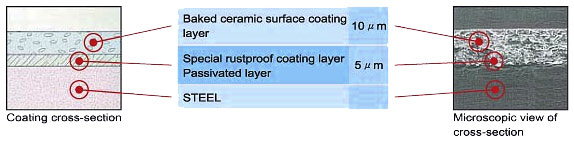
Coating layer | Rustproof structure |
Baked ceramic surface coating layer | Intrusion of corrosive factors is intercepted by the strong paint film made of ceramic materials. |
Special rustproof coating layer
|
Intrusion of corrosive factors is intercepted by pliability of RUSPERT organic paint that follows the expansion/contraction of substrate materials and also by its strong adhesion to the zinc plated surface. |
Passivated layer | Rustproof pigment contained in the RUSPERT paint produces an inactive film over the galvanized surface by chemical reaction. Thus, the galvanized surface is sufficiently passivated. |
RUSPERT
RUSPERT metal finish is the metal surface processing technology of high grade anti-corrosion consisting of 1st layer ; metallic zinc layer,2nd layer, high grade anti-corrosion chemical conversion film, and 3rd layer, baked ceramic surface coating.
The feature of RUSPERT is to join baked ceramic surface coating and chemical conversion film tightly together owing to bridging effect.
Furthermore, these layers are tightly joined together by means of chemical reactions, and such unique layer-combination brings stiff and fine combined coating films. RUSPERT treatment is not anti-corrosion by s single material, but by synergism of three layers, with which super rustproof quality is endowed.
Patent No. 1526310 Patent No. 1570203
Performance
Test item | Test result | Test method |
Hardness of paint film | Over 4H | Pencil hardness (peeling test) |
Adhesion | Nothing abnormal | Peeling test by adhesive tape on cross scribed test piece in 1mm width |
Acid resistance | Nothing abnormal | Immersion in 5% sulfuric acid solution for 24h |
Alkali resistance | Nothing abnormal | Immersion in 5% sodium hydroxide solution for 72h |
Heat resistance | Nothing abnormal | Exposure to 250°C heat for 1h |
Accelerated weathering | Free from red rust | In sunshine weather-0-meter for 1000h |
Contact corrosion to other metals | Obviously superior to galvanization(colored
chromating)and hot dip galvanizing. |
Corrosive investigation after Salt Mist Spray Test(JIS Z 2371)done comparatively on surface-treated steel bolts/nuts tightened on the stainless steel plate. |
Type of Processings
Type | Performance | Color Selection |
RUSPERT type I | S.S.T.500h
DIN 50018(0.2L)15 cycles |
Silver, Grey, Black, Other colors |
RUSPERT type II | S.S.T.1000h
DIN 50018(0.2L)15 cycles |
Silver, Grey, Black, Other colors |
RUSPERT type III | S.S.T.1000h
DIN 50018(2.0L)15 cycles |
Grey, Black |
RUSPERT on hot dip galvanizing | S.S.T.1000h
DIN 50018(0.2L)15 cycles |
Silver, Grey, Black, Other colors |
Coating and Rustproof Structure
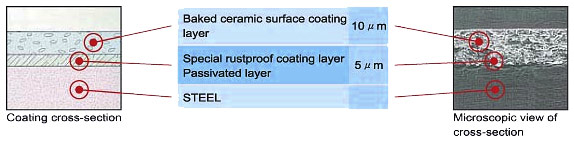
Coating layer | Rustproof structure |
Baked ceramic surface coating layer | Intrusion of corrosive factors is intercepted by the strong paint film made of ceramic materials. |
Special rustproof coating layer
|
Intrusion of corrosive factors is intercepted by pliability of RUSPERT organic paint that follows the expansion/contraction of substrate materials and also by its strong adhesion to the zinc plated surface. |
Passivated layer | Rustproof pigment contained in the RUSPERT paint produces an inactive film over the galvanized surface by chemical reaction. Thus, the galvanized surface is sufficiently passivated. |
RUSPERT
RUSPERT metal finish is the metal surface processing technology of high grade anti-corrosion consisting of 1st layer ; metallic zinc layer,2nd layer, high grade anti-corrosion chemical conversion film, and 3rd layer, baked ceramic surface coating.
The feature of RUSPERT is to join baked ceramic surface coating and chemical conversion film tightly together owing to bridging effect.
Furthermore, these layers are tightly joined together by means of chemical reactions, and such unique layer-combination brings stiff and fine combined coating films. RUSPERT treatment is not anti-corrosion by s single material, but by synergism of three layers, with which super rustproof quality is endowed.
Patent No. 1526310 Patent No. 1570203
Performance
Test item | Test result | Test method |
Hardness of paint film | Over 4H | Pencil hardness (peeling test) |
Adhesion | Nothing abnormal | Peeling test by adhesive tape on cross scribed test piece in 1mm width |
Acid resistance | Nothing abnormal | Immersion in 5% sulfuric acid solution for 24h |
Alkali resistance | Nothing abnormal | Immersion in 5% sodium hydroxide solution for 72h |
Heat resistance | Nothing abnormal | Exposure to 250°C heat for 1h |
Accelerated weathering | Free from red rust | In sunshine weather-0-meter for 1000h |
Contact corrosion to other metals | Obviously superior to galvanization(colored
chromating)and hot dip galvanizing. |
Corrosive investigation after Salt Mist Spray Test(JIS Z 2371)done comparatively on surface-treated steel bolts/nuts tightened on the stainless steel plate. |
Type of Processings
Type | Performance | Color Selection |
RUSPERT type I | S.S.T.500h
DIN 50018(0.2L)15 cycles |
Silver, Grey, Black, Other colors |
RUSPERT type II | S.S.T.1000h
DIN 50018(0.2L)15 cycles |
Silver, Grey, Black, Other colors |
RUSPERT type III | S.S.T.1000h
DIN 50018(2.0L)15 cycles |
Grey, Black |
RUSPERT on hot dip galvanizing | S.S.T.1000h
DIN 50018(0.2L)15 cycles |
Silver, Grey, Black, Other colors |
Coating and Rustproof Structure
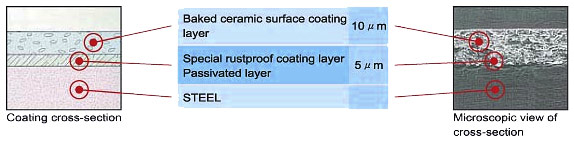
Coating layer | Rustproof structure |
Baked ceramic surface coating layer | Intrusion of corrosive factors is intercepted by the strong paint film made of ceramic materials. |
Special rustproof coating layer
|
Intrusion of corrosive factors is intercepted by pliability of RUSPERT organic paint that follows the expansion/contraction of substrate materials and also by its strong adhesion to the zinc plated surface. |
Passivated layer | Rustproof pigment contained in the RUSPERT paint produces an inactive film over the galvanized surface by chemical reaction. Thus, the galvanized surface is sufficiently passivated. |
RUSPERT
RUSPERT metal finish is the metal surface processing technology of high grade anti-corrosion consisting of 1st layer ; metallic zinc layer,2nd layer, high grade anti-corrosion chemical conversion film, and 3rd layer, baked ceramic surface coating.
The feature of RUSPERT is to join baked ceramic surface coating and chemical conversion film tightly together owing to bridging effect.
Furthermore, these layers are tightly joined together by means of chemical reactions, and such unique layer-combination brings stiff and fine combined coating films. RUSPERT treatment is not anti-corrosion by s single material, but by synergism of three layers, with which super rustproof quality is endowed.
Patent No. 1526310 Patent No. 1570203
Performance
Test item | Test result | Test method |
Hardness of paint film | Over 4H | Pencil hardness (peeling test) |
Adhesion | Nothing abnormal | Peeling test by adhesive tape on cross scribed test piece in 1mm width |
Acid resistance | Nothing abnormal | Immersion in 5% sulfuric acid solution for 24h |
Alkali resistance | Nothing abnormal | Immersion in 5% sodium hydroxide solution for 72h |
Heat resistance | Nothing abnormal | Exposure to 250°C heat for 1h |
Accelerated weathering | Free from red rust | In sunshine weather-0-meter for 1000h |
Contact corrosion to other metals | Obviously superior to galvanization(colored
chromating)and hot dip galvanizing. |
Corrosive investigation after Salt Mist Spray Test(JIS Z 2371)done comparatively on surface-treated steel bolts/nuts tightened on the stainless steel plate. |
Type of Processings
Type | Performance | Color Selection |
RUSPERT type I | S.S.T.500h
DIN 50018(0.2L)15 cycles |
Silver, Grey, Black, Other colors |
RUSPERT type II | S.S.T.1000h
DIN 50018(0.2L)15 cycles |
Silver, Grey, Black, Other colors |
RUSPERT type III | S.S.T.1000h
DIN 50018(2.0L)15 cycles |
Grey, Black |
RUSPERT on hot dip galvanizing | S.S.T.1000h
DIN 50018(0.2L)15 cycles |
Silver, Grey, Black, Other colors |
Coating and Rustproof Structure
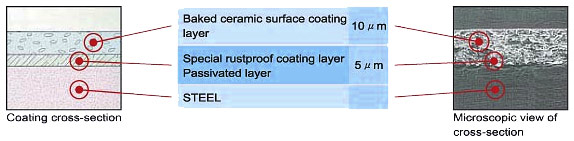
Coating layer | Rustproof structure |
Baked ceramic surface coating layer | Intrusion of corrosive factors is intercepted by the strong paint film made of ceramic materials. |
Special rustproof coating layer
|
Intrusion of corrosive factors is intercepted by pliability of RUSPERT organic paint that follows the expansion/contraction of substrate materials and also by its strong adhesion to the zinc plated surface. |
Passivated layer | Rustproof pigment contained in the RUSPERT paint produces an inactive film over the galvanized surface by chemical reaction. Thus, the galvanized surface is sufficiently passivated. |