迪斯克
迪斯克處理後的產品,包括高等的「無鉻酸」保護層,此保護多使用於產品避免水素脆性的發生。迪斯克處理包含2層塗裝,鋅泥先附著於鐵材上,而後面漆含有機和無機樹脂為主要成分,處理過程有浸漬和噴霧方式,再以180~250-°C高溫乾燥。
特長
1 | 高耐蝕性 | 鹽水噴霧試驗1000小時以上 |
2 | 無水素脆性 | 處理過程無需酸洗 |
3 | 無鉻酸 | 無含有害物質,如鉻酸、鉛、鎘,符合RoHS規範 |
4 | 低溫處理 | 低200溫度處理過程不會造成物質變化 |
5 | 耐藥物性 | 強烈耐酸雨 |
6 | 耐熱性 | 耐熱至600°C |
皮膜和防鏽架構
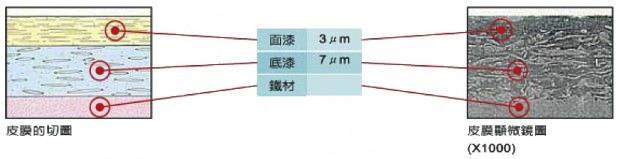
皮膜層 | 防鏽結構 |
面漆 | (樹脂層效果)樹脂包含在面漆內,緊密接附於主漆之上,以阻絕外在腐蝕因素和控制亞鉛流失。 |
底漆 | (亞鉛防鏽效果)鐵材因亞鉛保護,以避免腐蝕。 |
處理種類
種類 |
塗裝系列 | 預期防蝕性 | ||||
底漆 | 面漆 |
鹽水噴霧時間 (紅鏽產生時間) |
||||
料號 | 標準膜厚 | 料號 | 標準
膜厚 |
|||
1 | 低溫型 | DP-37 | ZT-200 | 500/1000小時 | ||
2 | 加重型 | DB-400 | ZT-200 | 1000/2000小時 | ||
3 | 耐熱型 | DB-400 | DB-500 | 1000/2000小時 | ||
4 | 低摩擦型 | DP-37 | ZT-300 | 500/1000小時 | ||
5 | 黑色型 | DBB-16 | DBT-05 | 500/1000小時 |
水素脆性試驗

測驗結果概要
水素分析結果 | |
表面處理種類 | 水素量(ppm) |
迪斯克處理 | 2 |
亞鋁電鍍(五彩) | 20 |
亞鋁電鍍(五彩和200乾燥5小時) | 14 |
未處理 | 2 |
結論 水素量的比較,迪斯克和未處理一樣。
DISGO
DISGO metal finish furnishes high grade chrome-free rustproof protection and is designed specially for steel products liable to be affected by delayed destruction ensuing from hydrogen embrittlement.
DISGO metal finish consists of 2 coatings. Zinc-flake rich paint undercoats the iron/steel substrate. coating over which is the top paint containing organic epoxy or non-organic silicate as major ingredient. The application is carried out by immersion in the top coating paint or its spraying and then dried in the heated atmosphere of 180°C to 250°C.
Features
1 | Superior corrosion resistance | Durable against Salt Spray Test over 1000 hours. |
2 | Free from hydrogen embrittlement | No acid is used for surface preparation. No electrolyzation is included in the processing.
No possibility, therefore, of delayed destruction by hydrogen embrittlement. |
3 | Chrome-free | Free from noxious materials such as chrome, lead and cadmium. |
4 | Low processing temperature | Low temperature curing of below 200°C gives no stress on the properties of treated articles. |
5 | Chemical- resistance | Available on order is DISGO specially prepared, strong against acidic rain. |
6 | Heat resistance | Heat resistance up to 600°C is available on request. |
Coating and Rustproof Structure
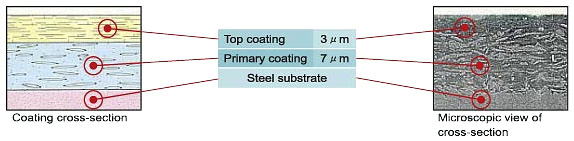
Coating layer | Rustproof structure |
Top coating | (Barrier effect by resin layers)The resin contained in the top coating seals the primary coating to shut off the intrusion of exterior corrosion factors and covers discontinuities and dents on the primary coating surface, and at the same time, controls speed of zinc dissolution. |
Primary coating | (Electrochemical rustproof effect by zinc)Iron/steel substrate is protected from corrosion by galvanic self-sacrificial effect of zinc. |
Type of Processings
Type |
Coating type | Anti-corrosion expectancy | ||||
Primary coating | Top coating | Salt Spray Test
(Up to appearance of red rust) |
||||
Paint | Thickness | Paint | Thickness | |||
1 | Low temperature
baking |
DP-37 | ZT-200 | 500/1000 h
|
||
2 | Super anti-corrosive | DB-400 | ZT-200 | 1000/2000 h | ||
3 | Heat-resisting | DB-400 | DB-500 | 1000/2000 h | ||
4 | Low-frictional | DP-37 | ZT-300 | 500/1000 h | ||
5 | Black color | DBB-16 | DBT-05 | 500/1000 h |
SSRT Test

Summary of test report
Result of hydrogen analysis | |
Type of surface treatment | Hydrogen(ppm) |
DISGO | 2 |
Galvanization(colored chromating) | 20 |
Galvanization(colored chromating and 5 hours baking at 200) | 14 |
Untreated | 2 |
Result: The amount of hydrogen detected in the DISGO treated test piece is same as that of untreated and intact sample.
DISGO
DISGO metal finish furnishes high grade chrome-free rustproof protection and is designed specially for steel products liable to be affected by delayed destruction ensuing from hydrogen embrittlement.
DISGO metal finish consists of 2 coatings. Zinc-flake rich paint undercoats the iron/steel substrate. coating over which is the top paint containing organic epoxy or non-organic silicate as major ingredient. The application is carried out by immersion in the top coating paint or its spraying and then dried in the heated atmosphere of 180°C to 250°C.
Features
1 | Superior corrosion resistance | Durable against Salt Spray Test over 1000 hours. |
2 | Free from hydrogen embrittlement | No acid is used for surface preparation. No electrolyzation is included in the processing.
No possibility, therefore, of delayed destruction by hydrogen embrittlement. |
3 | Chrome-free | Free from noxious materials such as chrome, lead and cadmium. |
4 | Low processing temperature | Low temperature curing of below 200°C gives no stress on the properties of treated articles. |
5 | Chemical- resistance | Available on order is DISGO specially prepared, strong against acidic rain. |
6 | Heat resistance | Heat resistance up to 600°C is available on request. |
Coating and Rustproof Structure
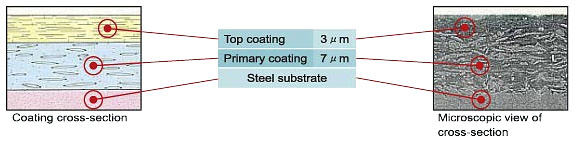
Coating layer | Rustproof structure |
Top coating | (Barrier effect by resin layers)The resin contained in the top coating seals the primary coating to shut off the intrusion of exterior corrosion factors and covers discontinuities and dents on the primary coating surface, and at the same time, controls speed of zinc dissolution. |
Primary coating | (Electrochemical rustproof effect by zinc)Iron/steel substrate is protected from corrosion by galvanic self-sacrificial effect of zinc. |
Type of Processings
Type |
Coating type | Anti-corrosion expectancy | ||||
Primary coating | Top coating | Salt Spray Test
(Up to appearance of red rust) |
||||
Paint | Thickness | Paint | Thickness | |||
1 | Low temperature
baking |
DP-37 | ZT-200 | 500/1000 h
|
||
2 | Super anti-corrosive | DB-400 | ZT-200 | 1000/2000 h | ||
3 | Heat-resisting | DB-400 | DB-500 | 1000/2000 h | ||
4 | Low-frictional | DP-37 | ZT-300 | 500/1000 h | ||
5 | Black color | DBB-16 | DBT-05 | 500/1000 h |
SSRT Test

Summary of test report
Result of hydrogen analysis | |
Type of surface treatment | Hydrogen(ppm) |
DISGO | 2 |
Galvanization(colored chromating) | 20 |
Galvanization(colored chromating and 5 hours baking at 200) | 14 |
Untreated | 2 |
Result: The amount of hydrogen detected in the DISGO treated test piece is same as that of untreated and intact sample.
DISGO
DISGO metal finish furnishes high grade chrome-free rustproof protection and is designed specially for steel products liable to be affected by delayed destruction ensuing from hydrogen embrittlement.
DISGO metal finish consists of 2 coatings. Zinc-flake rich paint undercoats the iron/steel substrate. coating over which is the top paint containing organic epoxy or non-organic silicate as major ingredient. The application is carried out by immersion in the top coating paint or its spraying and then dried in the heated atmosphere of 180°C to 250°C.
Features
1 | Superior corrosion resistance | Durable against Salt Spray Test over 1000 hours. |
2 | Free from hydrogen embrittlement | No acid is used for surface preparation. No electrolyzation is included in the processing.
No possibility, therefore, of delayed destruction by hydrogen embrittlement. |
3 | Chrome-free | Free from noxious materials such as chrome, lead and cadmium. |
4 | Low processing temperature | Low temperature curing of below 200°C gives no stress on the properties of treated articles. |
5 | Chemical- resistance | Available on order is DISGO specially prepared, strong against acidic rain. |
6 | Heat resistance | Heat resistance up to 600°C is available on request. |
Coating and Rustproof Structure
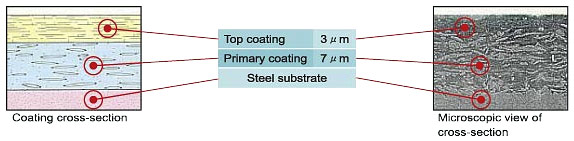
Coating layer | Rustproof structure |
Top coating | (Barrier effect by resin layers)The resin contained in the top coating seals the primary coating to shut off the intrusion of exterior corrosion factors and covers discontinuities and dents on the primary coating surface, and at the same time, controls speed of zinc dissolution. |
Primary coating | (Electrochemical rustproof effect by zinc)Iron/steel substrate is protected from corrosion by galvanic self-sacrificial effect of zinc. |
Type of Processings
Type |
Coating type | Anti-corrosion expectancy | ||||
Primary coating | Top coating | Salt Spray Test
(Up to appearance of red rust) |
||||
Paint | Thickness | Paint | Thickness | |||
1 | Low temperature
baking |
DP-37 | ZT-200 | 500/1000 h
|
||
2 | Super anti-corrosive | DB-400 | ZT-200 | 1000/2000 h | ||
3 | Heat-resisting | DB-400 | DB-500 | 1000/2000 h | ||
4 | Low-frictional | DP-37 | ZT-300 | 500/1000 h | ||
5 | Black color | DBB-16 | DBT-05 | 500/1000 h |
SSRT Test

Summary of test report
Result of hydrogen analysis | |
Type of surface treatment | Hydrogen(ppm) |
DISGO | 2 |
Galvanization(colored chromating) | 20 |
Galvanization(colored chromating and 5 hours baking at 200) | 14 |
Untreated | 2 |
Result: The amount of hydrogen detected in the DISGO treated test piece is same as that of untreated and intact sample.